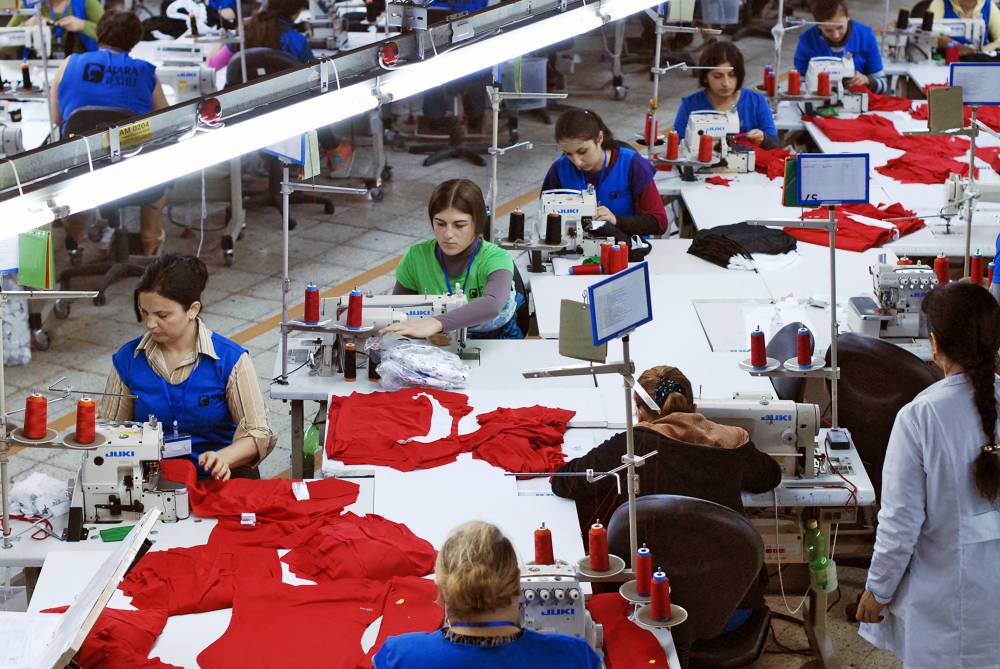
What Are The Main Components Of A Quality Manufacturing Business
The software for a quality manufacturing business should be designed to streamline and integrate all aspects of the manufacturing process, from raw material procurement to delivery of the finished product. It should provide a comprehensive view of the manufacturing operation, allowing management to make informed decisions about production schedules, resource allocation, and quality control.
Remote sensing software
The quality of a manufactured product is largely determined by the quality of the raw materials that go into it. To ensure that only the highest quality materials are used in their products, many manufacturers use remote sensing technology to inspect and grade raw materials before they are accepted for use in production.
Remote sensing software allows manufacturers to quickly and accurately assess the quality of raw materials, without the need for costly and time-consuming laboratory testing. This information can then be used to make decisions about which suppliers to source materials from, and what grades of material should be used in production.
In addition to helping to ensure the quality of raw materials, remote sensing software can also be used to monitor the manufacturing process itself. The photonics team at https://www.labsphere.com/ recommend this software to improve the characterization and calibration of products. By installing sensors at key points in the production line, manufacturers can track the progress of each individual product as it moves through the factory. This information can be used to identify bottlenecks in the manufacturing process and make necessary adjustments to improve efficiency.
The benefits of using remote sensing software in a quality manufacturing business are clear. By streamlining the inspection and grading of raw materials, and by providing real-time data on the progress of individual products through the manufacturing process, businesses can save time and money while ensuring that their products are of the highest possible quality.
Enterprise Resource Planning (ERP) software
ERP software is the backbone of any manufacturing operation, providing a central repository for all data related to the business. It includes modules for accounting, finance, inventory management, human resources, and customer relationship management. ERP software should be designed specifically for manufacturing businesses, with functionality to support the unique needs of this sector.
Computer-Aided Design (CAD) software
CAD software is used by engineers to design products and create production drawings. It is an essential tool for creating accurate models and assemblies that can be used in the manufacturing process. CAD software should be integrated with ERP and PLM software to allow data to flow seamlessly between departments.
Manufacturing Execution Systems (MES) software
MES software is used to manage and control the manufacturing process, from raw material procurement to delivery of the finished product. It includes modules for production scheduling, quality control, and machine monitoring. MES software should be integrated with ERP and PLM software to provide a complete view of the manufacturing operation.
Product Lifecycle Management (PLM) software
PLM software is used to manage the data associated with a product throughout its lifecycle, from initial conception through to final disposal. It includes modules for product development, project management, and regulatory compliance. PLM software should be integrated with ERP and CAD software to allow data to flow seamlessly between departments.
These four software components are essential for a quality manufacturing business. They should be designed to work together seamlessly, providing a comprehensive view of the manufacturing operation. By integrating these systems, businesses can improve efficiency, reduce costs, and optimize the manufacturing process.