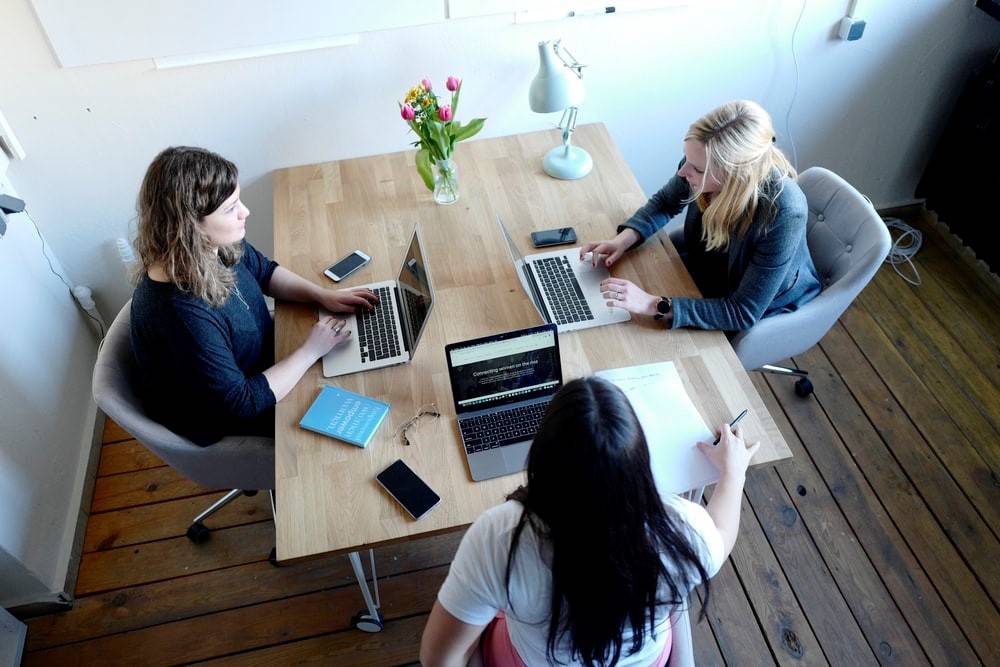
Types of PLCs (Programmable Logic Controllers)
Introduction to PLCs
Programmable Logic Controllers (PLCs) are integral components in industrial automation, enabling efficient and reliable control of manufacturing processes. They are digital computers used for automation of electromechanical processes, such as control of machinery on factory assembly lines, amusement rides, or light fixtures. Their robustness and versatility make them essential in numerous industries. This article delves into the various types of PLCs, their functionalities, and their applications.
Types of PLCs
PLCs are categorized based on their size, functionality, and application requirements. Understanding these types helps in selecting the most suitable PLC for a specific industrial task.
1. Compact PLCs
Compact PLCs are all-in-one units where the power supply, CPU, and input/output (I/O) modules are housed in a single enclosure. They are ideal for small to medium-sized applications where space is limited. Compact PLCs are cost-effective and easy to install, making them suitable for straightforward automation tasks.
Key Features:
- Integrated design
- Limited expandability
- Suitable for small-scale applications
- Cost-effective solution
Applications:
2. Modular PLCs
Modular PLCs consist of separate modules for power supply, CPU, and I/O, which can be combined in various configurations to suit different applications. This modularity provides greater flexibility and expandability compared to compact PLCs. They are well-suited for complex and large-scale industrial automation projects.
Key Features:
- Highly flexible and expandable
- Customizable configurations
- Suitable for large-scale applications
- Higher initial cost but scalable
Applications:
- Complex process control
- Large manufacturing plants
- Distributed control systems
3. Rack-Mounted PLCs
Rack-Mounted PLCs are a type of modular PLC where the modules are mounted on a rack. This setup allows for easy maintenance and replacement of individual modules without affecting the entire system. Rack-mounted PLCs are typically used in environments that require robust and reliable performance.
Key Features:
- Modular design with rack-mounted modules
- High reliability and ease of maintenance
- Suitable for large-scale and mission-critical applications
- Higher initial investment
Applications:
- Power plants
- Oil and gas industries
- Large-scale automation systems
Specialized PLCs
In addition to the general categories, there are specialized PLCs designed for specific applications and industries.
1. Safety PLCs
Safety PLCs are designed with built-in safety features to perform safety-critical functions in industrial environments. They ensure that machinery and processes operate within safe parameters, reducing the risk of accidents and equipment damage.
Key Features:
- Enhanced safety features
- Compliance with safety standards (e.g., SIL, ISO 13849)
- Dual-channel architecture for redundancy
- Suitable for safety-critical applications
Applications:
- Emergency shutdown systems
- Safety interlocking
- Machine guarding
2. Motion Control PLCs
Motion Control PLCs are tailored for precise control of motion in machinery and robotics. They are equipped with advanced algorithms for controlling speed, position, and torque, making them essential in applications that require high precision.
Key Features:
- Advanced motion control algorithms
- High-speed processing
- Integration with servo drives and motors
- Suitable for high-precision applications
Applications:
- Robotics
- CNC machines
- Packaging machinery
3. Networked PLCs
Networked PLCs are designed to communicate over various industrial networks, allowing for distributed control and monitoring. They can be integrated with other PLCs and devices in a network, facilitating seamless data exchange and coordinated control.
Key Features:
- Support for various communication protocols (e.g., Ethernet/IP, Modbus, Profibus)
- Distributed control capabilities
- Enhanced data exchange and interoperability
- Suitable for networked environments
Applications:
- Distributed control systems
- Remote monitoring and control
- Industrial IoT (IIoT) applications
Choosing the Right PLC
Selecting the appropriate PLC depends on several factors, including the complexity of the automation task, the scale of the application, and specific industry requirements. Here are some considerations to guide the selection process:
1. Application Requirements
Identify the specific needs of the application, such as the number of I/O points, processing speed, and required communication protocols. This helps in determining whether a compact, modular, or specialized PLC is most suitable.
2. Scalability and Flexibility
Consider the future expansion needs of the application. Modular and rack-mounted PLCs offer greater flexibility and scalability, making them ideal for applications that may grow over time.
3. Environmental Conditions
Evaluate the environmental conditions where the PLC will operate, such as temperature, humidity, and exposure to dust or chemicals. Ruggedized PLCs are available for harsh environments, ensuring reliable operation under challenging conditions.
4. Safety and Compliance
For safety-critical applications, choose PLCs that comply with relevant safety standards and offer built-in safety features. Safety PLCs provide additional layers of protection, ensuring safe and reliable operation.
5. Cost Considerations
Balance the initial cost of the PLC with the long-term benefits, such as ease of maintenance, expandability, and reduced downtime. While compact PLCs are cost-effective for small applications, modular and rack-mounted PLCs offer better value for larger and more complex systems.
Conclusion
PLCs are versatile and essential components in industrial automation, offering a range of options to suit different applications and industries. Understanding the types of PLCs and their specific features and applications helps in selecting the most appropriate PLC for any given task. Whether it's a compact PLC for a simple automation task or a modular PLC for a large-scale industrial system, the right choice can significantly enhance efficiency, reliability, and safety in industrial processes.
Related Courses and Certification
Also Online IT Certification Courses & Online Technical Certificate Programs