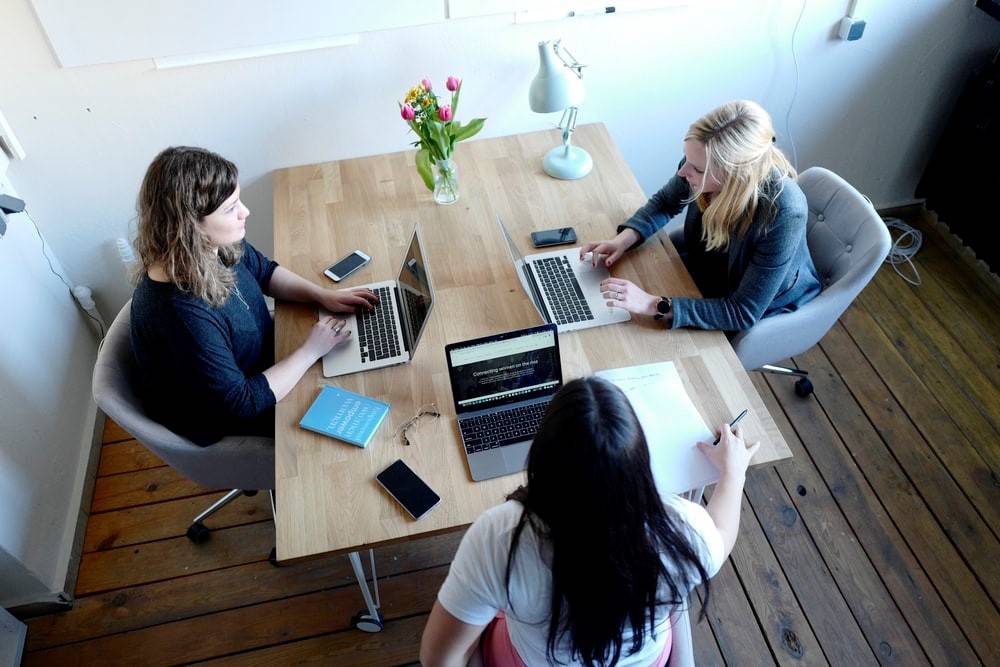
Direct Costs & Indirect Costs: Complete Guide + Examples
Cost allocation is the process of distributing your indirect costs among specific departments or projects. What is considered an indirect cost for one company might be considered a direct cost for another. And, one employee’s salary might be an indirect cost while another’s is a direct cost. For example, an employee on an assembly line receives wages that are considered direct costs. But an employee who works as a secretary in the same company would receive wages that are considered indirect expenses.
Irrespective of whatever you decide your strategy to be, it should be based on a thorough understanding of product costs and other factors. This is because while the fixed costs that are included in the production costs remain constant, variable costs do not. We hope that the detailed explanations, examples, and FAQs provided here have shed light on the complexities of manufacturing costs and will serve as valuable resources for businesses in the manufacturing sector. By diligently calculating and managing manufacturing costs, companies can enhance cost efficiency, maintain competitiveness, and improve their bottom line. “When a manufacturer begins the production process, the costs incurred to create the products are initially recorded as assets in the form of WIP inventory. Cost control, according to Fabrizi, is one of the top benefits of calculating manufacturing costs.
For example, a maintenance technician’s team is driven by factors including the number and complexity of assets to be maintained, their criticality for production, and their loss profile. The more production is increased, the greater the amount of time that must be spent on these activities. In fact, this software will also help you determine the optimal level of safety stock for your business.
When an entity accepts a grant, such as government funding, the funding guidelines typically stipulate what qualifies as a direct versus indirect cost, along with any threshold amounts for each cost type. Understanding the true total cost of producing goods and services enables a business to make sound decisions, particularly in the areas of pricing, budgeting, operational efficiency, and taxation. To make the matter even more complicated, direct and indirect expense categories can vary among different industries and even within the same business. Companies that realize the potential from improving indirect operations could develop a competitive edge and build up resilience to better face the instabilities of today’s market. A two-week top-down benchmarking exercise, backed by two weeks of shopfloor observations and maturity assessments, provided targeted insights into the most significant improvement opportunities.
Knowing the total cost of manufacturing a product can help ensure that products are priced appropriately and that businesses are making a profit. This is because companies can sell their products at a lower price, making them more affordable to consumers. Additionally, lower costs can help companies expand their operations and hire more workers — boosting the economy by creating new jobs and increasing consumer spending. When you know the total cost of manufacturing a product, you can find ways to reduce that cost more easily.
Indirect cost examples
Direct labor could average out to $10 per unit, as they produce several per hour. Whatever you do, watch out for counting costs twice by not understanding this. One other staff member – a specialist coffee roaster – earns $35 per hour, with payroll taxes of $5 per hour and $3 fringe benefit costs per hour. Richard has two staff members who earn $25 per hour, their payroll taxes costs $5 per hour and they have $3 worth of fringe benefit costs per hour. Hence, mastering cost management is an important part of running and growing a business.
- Indirect costs are subsidiary material costs, such as shop supply costs, perishable tools and equipment costs.
- The first distinction is between the three major costs components of manufacturing a product — these can be direct or indirect.
- According to McKinsey’s research, cutting down manufacturing costs, in addition to boosting productivity, is the key for manufacturing companies to remain competitive.
- This is where a manufacturing time tracking app, such as Clockify, comes in handy.
Yet indirect functions are essential in driving efficiency in day-to-day factory operations, raising the stakes for leaders looking to make changes. Moreover, the sheer range of tasks in indirect operations can make improvements more difficult to scale; improvements in the most meaningful, long-term activities can appear especially difficult to replicate. As a result, leaders can all too easily opt for the seemingly easier option of retaining a larger support team, with efficiency initiatives focused only on shopfloor processes. Other examples include packaging materials and freight costs on raw materials. If this employee worked on all three jobs for eight hours a day, then she would be spending 24 hours per week on indirect labor activities.
Direct and Indirect Materials Cost FAQs
Consider how valuable the expense is to operating your business and come up with ways to slash the price. But, the money you pay towards rent does not go towards producing a specific product. Instead, rent payments make it possible to produce all your products and run your business. Ultimately, improving efficiency in your manufacturing process is important for ensuring that your products are of the highest quality and meet customer demands promptly.
What are the benefits of using the total manufacturing cost formula?
Allocating overhead helps you to identify areas to improve efficiency and reduce costs. It is important for pricing decisions because by incorporating indirect costs into pricing, you can cover costs by effectively pricing inventory stock to improve profitability. As an indirect cost, manufacturing overhead it is challenging to assign overhead costs to each of the units produced.
Fixed Costs
Now you can determine the manufacturing overhead rate — this is the percentage of your monthly revenue that goes towards paying for overheads each month. To do this, divide the monthly manufacturing overhead by the value of your monthly sales, multiplying that by 100. It is not uncommon to identify and unlock a 15 to 25 percent optimization potential in indirect functions, which can translate to a sizeable impact on the bottom line. Labor costs are one of the highest contributors in significantly driving up your total manufacturing costs. Thus, it makes sense for your business to cut back on this area and thus make your manufacturing lean.
Direct costs need to be properly tracked, measured and valued so they can be correctly attributed directly to a specific cost object, such as a product, service or business unit. Calibration takes into account the specific factors that have an effect on the conversion method of single entry system or transaction approach scope and complexity of tasks to be performed in an indirect support function. This driver-based logic is common practice in benchmarking sales, general, and administrative (SG&A) costs and could be applied equally well to improve indirect operations.
As the manufacturing process involves raw materials and finished goods, all of these are considered assets. The materials that are yet to be assembled /processed and sold are considered work-in-process or work-in-progress (WIP) inventory. You can reduce other indirect costs, like advertising, by engaging customers through social media or using other inexpensive marketing ideas. You will also have direct costs, which are expenses you can assign to the production of a specific product or service. The above expenses are considered indirect if they cannot be applied toward a single product or service. Office supplies, for example, are indirect if they are not direct materials to create products.
A manufacturing company initially purchased individual components from different vendors and assembled them in-house. As the company decided to assemble the components themselves, they found that the costs of managing the assembly line and the transportation were increasing significantly. Manufacturing cost calculation gives an accurate view of the costs allowing companies to eliminate irrelevant costs and optimize resource utilization to boost profitability. For instance, let’s say the hourly rate a manufacturing company pays to its employees is $30. As employees use Clockify to clock in and out, employers gain insights into the total number of hours each employee worked on each production line. Tracking the number of hours each employee works on the production line can be tricky.
SIIT Courses and Certification
Also Online IT Certification Courses & Online Technical Certificate Programs