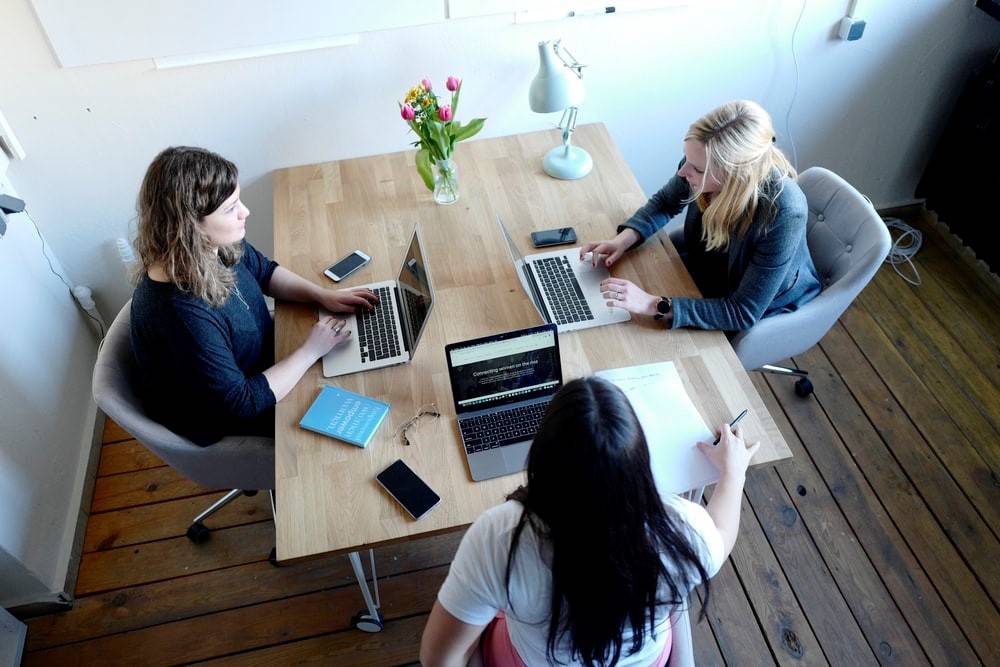
Breaking Free From Common SAP PM Implementation Mistakes
SAP Plant Maintenance (PM) is a powerful tool, but its implementation can be fraught with pitfalls. This article dives deep into common mistakes, offering practical solutions and innovative strategies to ensure a smooth and successful deployment. We’ll explore crucial areas often overlooked, leading to project delays, budget overruns, and ultimately, a system that fails to deliver its promised value.
Mastering Data Migration: Avoiding the Pitfalls of Incomplete or Inaccurate Data
Data migration is a critical phase, often underestimated. Inaccurate or incomplete data can lead to inaccurate reporting, flawed maintenance planning, and ultimately, equipment failures. One common mistake is failing to thoroughly cleanse and validate data before migration. A case study of a manufacturing company showed that inaccurate asset information led to a 15% increase in unplanned downtime. Another example involved a chemical plant where outdated maintenance schedules, due to poor data migration, resulted in a costly emergency shutdown. Effective data migration necessitates a robust data cleansing process, involving data profiling, standardization, and validation. Tools such as SAP Landscape Transformation (SLT) can aid this process. However, success demands a clear understanding of data relationships, effective data mapping, and rigorous testing. Successful implementations involve establishing a clear data governance framework. This includes defined roles and responsibilities, data quality metrics, and processes for addressing data discrepancies. Data quality rules and automated checks are also essential, ensuring consistency and accuracy. Regular reviews and audits are crucial to proactively identify and resolve issues. Furthermore, investing in comprehensive data mapping and using tools like SAP Data Services can improve the accuracy and reliability of the data migration process.
Optimizing Work Order Management: Beyond Basic Functionality
Many organizations treat work order management as a basic task. However, optimizing this aspect is crucial for efficiency. A common error is neglecting proper work order prioritization, leading to delayed repairs and production disruptions. For instance, a food processing company experienced significant production delays due to poor work order prioritization. Prioritizing based on criticality and impact on production, combined with efficient scheduling algorithms, improves overall effectiveness. Another example is a power utility that improved its response time to outages by 20% by implementing a more sophisticated work order management system. This included features such as automated notifications, real-time tracking, and mobile access for technicians. Real-time tracking tools offer significant improvements, enabling better resource allocation and enhancing overall responsiveness. Sophisticated routing algorithms can also optimize the assignment of work orders to technicians based on factors like skill sets, location, and workload. The key is to move beyond the basic functionalities and leverage the full potential of the system through features such as mobile accessibility, real-time data dashboards, and intelligent scheduling.
Effective Reporting and Analysis: Unveiling Hidden Insights
The power of SAP PM lies not only in its transactional capabilities, but also in its analytical potential. A frequent oversight is failing to leverage the reporting and analysis features effectively. Consider a case study in which a large automotive manufacturer struggled with maintenance costs. By implementing detailed analysis reports, they identified bottlenecks and inefficiencies, resulting in a 10% reduction in costs. Another example from a chemical processing plant showcased that leveraging predictive maintenance analytics led to a 15% reduction in unplanned downtime. This emphasizes the importance of proactive maintenance strategies. Advanced reporting tools within SAP PM can help extract valuable insights into maintenance performance, enabling data-driven decision-making. Customizing reports to focus on key performance indicators (KPIs) like equipment downtime, maintenance costs, and Mean Time To Repair (MTTR) provides crucial insights. Integrating SAP PM data with other SAP modules, such as Production Planning (PP) or Enterprise Resource Planning (ERP), facilitates a holistic view of operations. Data visualization tools can present complex data in a user-friendly format, enabling faster identification of trends and patterns. Implementing such solutions can transform reactive maintenance strategies into proactive ones, improving efficiency and reducing costs.
User Adoption and Training: Empowering Your Workforce
A successful SAP PM implementation relies heavily on user adoption. Insufficient training and lack of user engagement frequently lead to system underutilization and frustration. A manufacturing company experienced low user adoption due to inadequate training. Subsequently, they revised their training program, incorporating hands-on workshops and targeted training sessions. The result? A significant improvement in user satisfaction and system utilization. Another example involved a healthcare facility, where user-friendly interfaces and tailored training led to a smoother transition and better system acceptance. Effective training should cover various aspects of the system. This includes initial onboarding, regular refresher courses, and ongoing support. Designing user-friendly interfaces plays a crucial role. This entails simplifying processes and reducing the complexity of navigation. The use of interactive tutorials, online help resources, and providing a user-friendly design reduces the learning curve and improves the overall user experience. Furthermore, integrating feedback mechanisms into the training program to make it iterative and continually improve user experience is essential. Encouraging active participation and providing continuous support minimizes the challenges associated with user adoption.
Integration with Other SAP Modules: Leveraging the Ecosystem
SAP PM doesn't operate in isolation. Integrating it with other SAP modules, such as Plant Maintenance (PM), Production Planning (PP), and Materials Management (MM), is critical for efficient operations. A case study of a logistics company revealed that integrating SAP PM with SAP Transportation Management (TM) optimized resource allocation and improved delivery times. Another instance involved a pharmaceutical company where integrating SAP PM with SAP Quality Management (QM) improved the quality control processes and ensured compliance with regulatory standards. Successful integration streamlines workflows, improves data consistency, and reduces manual intervention. For example, automatic updates of material information from MM to PM can ensure that maintenance activities utilize the most accurate data. Seamless integration eliminates data redundancy and improves decision-making across various departments. Moreover, it helps to establish a unified view of operations, enhancing overall organizational efficiency and transparency. Effective integration can also enable streamlined reporting and analysis, enhancing the overall effectiveness of data-driven insights. This integrated approach significantly contributes to improved operational efficiency and reduced costs.
Conclusion
Successful SAP PM implementation requires meticulous planning, execution, and ongoing optimization. Addressing the common mistakes outlined above – from data migration challenges to user adoption issues and integration complexities – is critical for reaping the full benefits of this powerful system. By proactively addressing these challenges, organizations can ensure that their SAP PM investment delivers significant returns, driving operational efficiency, reducing costs, and improving overall maintenance performance. Remember, a successful SAP PM journey is not a destination, but an ongoing process of continuous improvement and optimization. The key is to embrace continuous improvement and regularly assess the system’s performance to ensure alignment with evolving business needs.