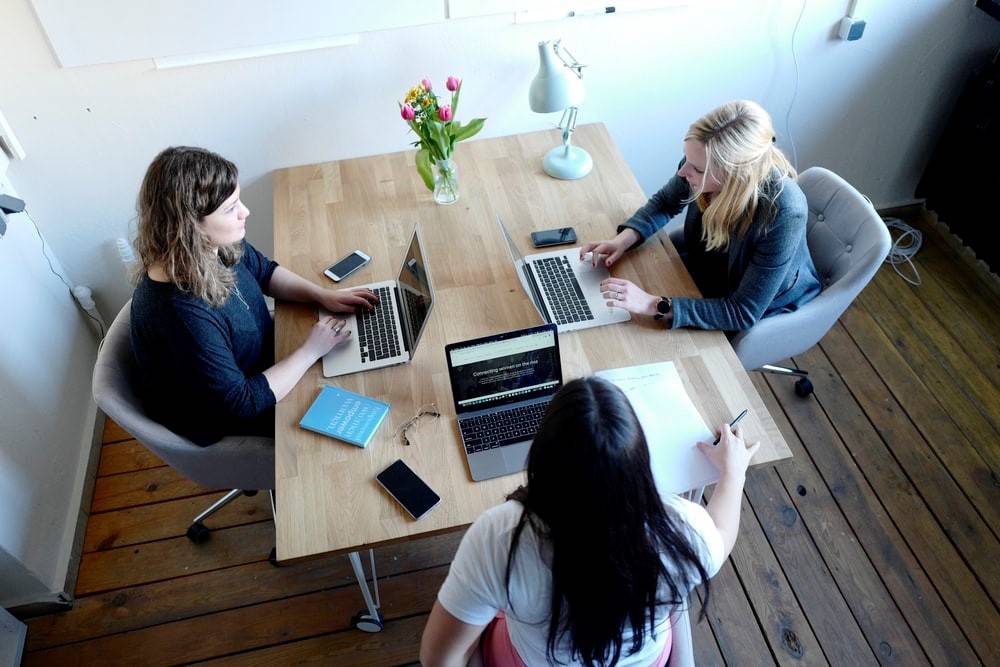
Answered: Product costs are also called:
He has a CPA license in the Philippines and a BS in Accountancy graduate at Silliman University. Knowing the true costs of development can help you determine what features to build, whether for an MVP or for your next major update. This may seem like an additional cost at first, but quality assurance (QA) is crucial to spotting errors and bugs. Without QA, your development costs could increase and your timeline can extend further than originally anticipated. Evaluating your expenses can help you determine whether you’re getting the most value out of them or need to consider alternatives.
- Selling costs can vary somewhat with product sales levels, especially if sales commissions are a large part of this expenditure.
- Companies like Ford and General Electric began using cost management techniques to improve their operations and increase profitability.
- Collaboration between departments, such as finance and production, can help ensure that the costs are accurately tracked and allocated.
- It can be hard to strike a balance between prices that are attractive, while still suggesting value to customers, but it’ll be impossible if you don’t keep your eye on the market.
Instead of combining shipping, separate the cost so the product price seems lower. “The Rule of 100” suggests that if you’re running a sale on items costing under $100, you should show it as a percentage discount. Whereas, if you’re running a sale on items costing over $100, you should show the savings in dollars. We’ll show you how to calculate your costs soon, but first it’s time for some competitor research.
Examples of product costs are direct materials, direct labor, and allocated factory overhead. Examples of period costs are general and administrative expenses, such as rent, office depreciation, office supplies, and utilities. In managerial and cost accounting, period costs refer to costs that are not tied to or related to the production of inventory.
Accounting Treatment of Product and Period Cost
This also determines how your audience perceives you, which ultimately affects your pricing. Determine your markups and profit margin to set the perfect price and increase your bottom line with our product pricing calculator. Here, we’ll walk you through a few of those formulas and some steps you can take to create successful pricing strategies for your product, whether you sell wholesale, retail, or both. It can be hard to strike a balance between prices that are attractive, while still suggesting value to customers, but it’ll be impossible if you don’t keep your eye on the market. This is called charm pricing, and is a tried and tested method used by most sellers. Don’t miss out – go through and change any round prices so they cost one cent less.
- Now that you have a better understanding of the formulas used to calculate product pricing, it’s time to build your own pricing strategy.
- Net sales for 2010 totaled $57,800,000,000, resulting in operating profits of $6,300,000,000.
- This is just good practice, but if you’re running a sale, you should always show the original price next to the new sale price.
- With this information, you can make informed decisions about pricing strategies, potential profitability, and areas to optimize costs during the development process.
Austin has been working with Ernst & Young for over four years, starting as a senior consultant before being promoted to a manager. At EY, he focuses on strategy, process and operations improvement, and business transformation consulting services focused on health provider, payer, and public health organizations. Austin specializes in the health industry but supports clients across multiple industries. There you have it – we’ve taken you through the key points of setting the right pricing for your products.
What is product cost and how to calculate (with example)
For a retailer, the product costs would include the supplies purchased from a supplier and any other costs involved in bringing their goods to market. In short, any costs incurred in the process of acquiring or manufacturing a product are considered product costs. While product costs are directly tied to the creation and development of a software product or technology solution. Period costs are the expenses that a company incurs during a specific accounting period but aren’t directly related to the product’s development. To calculate variable manufacturing overhead costs, we need to know the total direct labor hours worked. Examples of period costs include selling and marketing expenses, administrative expenses (SG&A), and research and development expenses (R&D).
Price Like a Pro: Adapting Your Pricing Strategy to Any Market Conditions
Thus, these too are considered period costs and reported on the income statement as an expense. Overhead or sales, general, and administrative (SG&A) costs are considered period costs. SG&A includes costs of the corporate office, selling, marketing, and the overall administration of company business. All manufacturing costs that are easily traceable to a product are classified as either direct materials or direct labor. All other manufacturing costs are classified as manufacturing overhead.
Selling Costs
These costs have two components—selling costs and general and administrative costs—which are described next. In management accounting, there exists a classification of costs based on their capitalization as a part of finished goods inventory or expense as incurred. The classification segregates the costs as product costs and period costs. PepsiCo, Inc., produces more than 500 products under several different brand names, including Frito-Lay, Pepsi-Cola, Gatorade, Tropicana, and Quaker.
Otherwise, you won’t know where the money went and how to avoid it in the future. Rent and utilities are classic examples of something that makes product creation possible but still doesn’t necessarily participate in the process itself. The first step in activity-based costing is to identify all the different activities performed in an organization and then assign an overhead cost to each activity. This can be an effective way to save on labor costs while still maintaining quality standards.
Why is it important to distinguish product costs and period costs?
In this case, different buyers in different situations pay different prices for the same product. When setting your wholesale price, first multiply your cost of goods by two. The simplest way to determine the price of a product is cost-plus pricing, also called markup pricing. This means working out how much it costs in total to make your product, then adding your markup percentage. You’re probably thinking we’re stating the obvious, but it’s easy to get drawn into competitor price wars. There’s no point in selling your products cheaper than anyone else on the market, if you can’t afford to keep your business running.
Create a minimal viable product (MVP)
These are direct (the first two) and indirect (the last) costs of production. Once you calculate all these costs, divide them by the total number of units produced how to calculate present value of future cash flows to get your final product cost. This number is essential because it will help you determine how much you need to charge for your product to make a profit.
Understanding how much you pay for stuff is the first step to reducing your expenses. Product cost is an essential factor in determining a company’s profitability. To maximize profitability, companies must carefully control their production costs while also striving to produce high-quality products that customers are willing to pay for. The raw materials inventory27 account records the cost of materials not yet put into production. For Custom Furniture Company, this account includes items such as wood, brackets, screws, nails, glue, lacquer, and sandpaper.
Net sales for 2010 totaled $57,800,000,000, resulting in operating profits of $6,300,000,000. Cost of sales represented the highest cost on the income statement at $26,600,000,000. The second highest cost on the income statement—selling and general and administrative expenses—totaled $22,800,000,000. These expenses are period costs, meaning they must be expensed in the period in which they are incurred. Costs that are not related to the production of goods are called nonmanufacturing costs; they are also referred to as period costs.
SIIT Courses and Certification
Also Online IT Certification Courses & Online Technical Certificate Programs