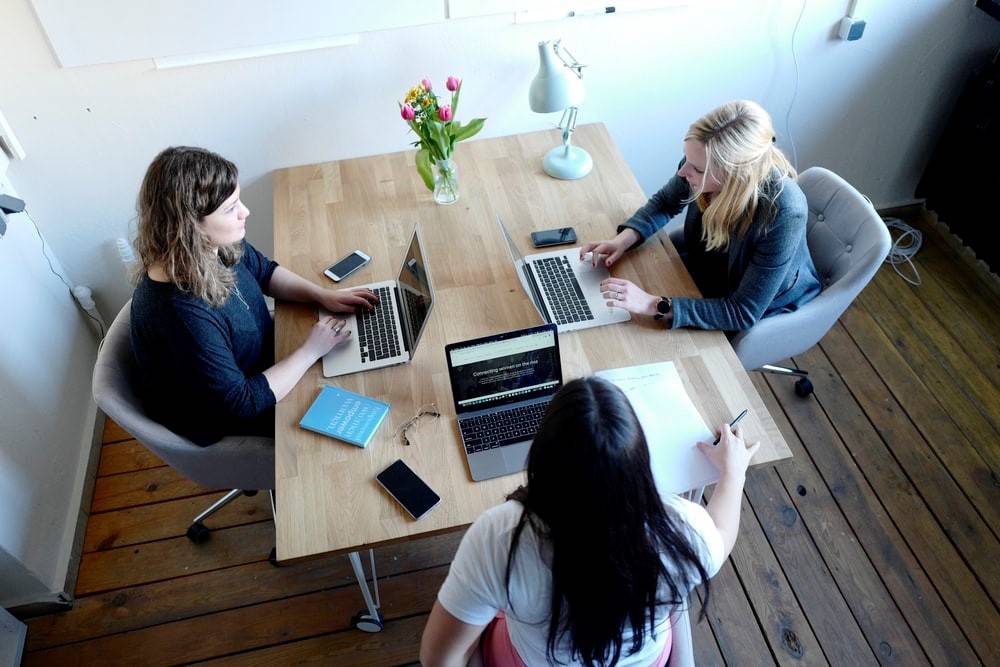
How to Implement MIS for Improving Product Lifecycle Management
Implementing a Management Information System (MIS) for improving Product Lifecycle Management (PLM) involves leveraging data-driven insights, collaboration tools, and process automation to streamline product development, enhance quality, and accelerate time-to-market. Here's how to effectively implement an MIS for this purpose:
1. Define Product Lifecycle Stages:
- Define and map out the different stages of the product lifecycle, including ideation, design, development, testing, manufacturing, launch, and post-launch support.
- Identify key milestones, deliverables, and dependencies for each stage to establish a structured framework for PLM.
2. Centralize Product Data and Documentation:
- Implement a centralized repository within the MIS to store product-related data, documents, specifications, and revisions.
- Enable version control and access control mechanisms to ensure data integrity and security throughout the product lifecycle.
3. Enable Cross-Functional Collaboration:
- Facilitate cross-functional collaboration and communication among teams involved in product development, such as engineering, design, manufacturing, marketing, and sales.
- Provide collaboration tools, such as shared workspaces, project management software, and communication channels, within the MIS to foster teamwork and knowledge sharing.
4. Streamline Design and Development Processes:
- Streamline design and development processes within the MIS by automating workflows, approvals, and change management procedures.
- Enable real-time collaboration on design files, prototypes, and specifications to accelerate iteration cycles and minimize errors.
5. Implement Quality Management Systems:
- Implement quality management systems within the MIS to ensure product quality and compliance with regulatory standards and customer requirements.
- Track and manage quality metrics, non-conformance incidents, corrective actions, and audits throughout the product lifecycle.
6. Integrate with Supply Chain and Manufacturing Systems:
- Integrate the MIS with supply chain management (SCM) and manufacturing execution systems (MES) to optimize production planning, inventory management, and resource allocation.
- Enable real-time visibility into supply chain operations, supplier performance, and production schedules to identify bottlenecks and mitigate risks.
7. Capture and Analyze Product Data:
- Capture and analyze product data within the MIS to gain insights into customer preferences, market trends, and competitive landscape.
- Utilize data analytics and business intelligence tools to identify opportunities for product innovation, differentiation, and optimization.
8. Enable Regulatory Compliance and Documentation:
- Ensure regulatory compliance throughout the product lifecycle by integrating compliance management features into the MIS.
- Maintain comprehensive documentation, regulatory filings, and audit trails to demonstrate compliance with industry standards and regulatory requirements.
9. Implement Product Lifecycle Costing:
- Implement product lifecycle costing capabilities within the MIS to track costs associated with design, development, manufacturing, and support activities.
- Calculate total cost of ownership (TCO), return on investment (ROI), and profitability metrics to inform decision-making and resource allocation.
10. Enable Customer Feedback and Iterative Improvement:
- Capture customer feedback and insights within the MIS to inform product enhancements, feature prioritization, and future development initiatives.
- Implement feedback loops and customer engagement channels to solicit input, gather requirements, and validate product concepts throughout the lifecycle.
11. Monitor and Measure Performance:
- Monitor and measure key performance indicators (KPIs) related to product lifecycle management, such as time-to-market, product quality, and customer satisfaction.
- Use performance metrics and benchmarks to evaluate the effectiveness of PLM processes and identify areas for improvement.
12. Continuously Iterate and Improve:
- Continuously iterate and improve PLM processes and systems based on feedback, performance data, and lessons learned.
- Foster a culture of innovation, agility, and continuous improvement within the organization to drive product excellence and competitive advantage.
By implementing a Management Information System (MIS) for improving Product Lifecycle Management (PLM), organizations can streamline processes, enhance collaboration, and drive innovation across the entire product lifecycle, ultimately delivering better products to market faster and more efficiently.
SIIT Courses and Certification
Also Online IT Certification Courses & Online Technical Certificate Programs
SIIT is on a mission to make technology education and professional training more accessible, so more people can show off their talents and take their tech careers to the next level. All courses are tailored to meet individual specific career needs, leading to Tech Skills Acquisition and Professional Certification.
Student Login
Login & Study At Your Pace
500+ Relevant Tech Courses
700,000+ Enrolled Students
Jobs Vacancy
The Jobs portal provides you with real time Jobs Opening and Vacancy Updates curated globally. Start applying for your dream job with ease in any location you choose.
Learn More >>