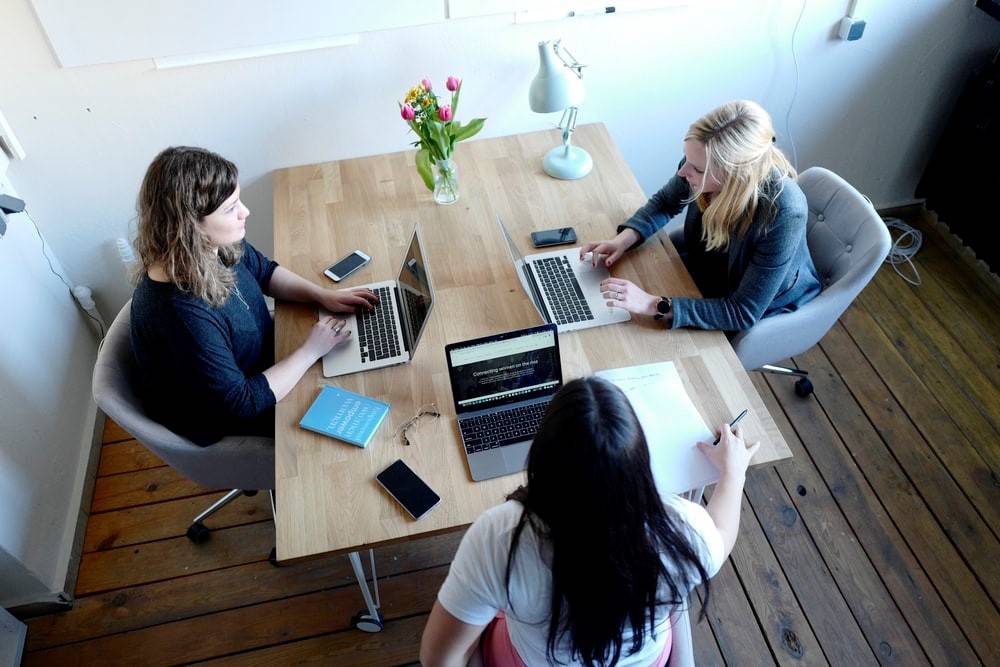
What are the top ways to choose safe electrical insulating rubber mat?
Electrical insulating rubber mats, in turn, provide workers with shock and arc flash protection for both people and equipment. Conductive surfaces are blocked by these mats, decreasing the risk of accidents in electrically equipped areas. The proper insulating rubber mat selection is a crucial factor for workplace safety and regulatory compliance.
To choose a product, which reduces electrical dangers, check the voltage rating, material composition, thickness and surface roughness. A set of regulations and best practices can ensure workplaces are safer, workers are protected, lost productivity and injuries are minimized. This article will help the decision-makers select the most reliable electrical insulating rubber strip.
What are electrical insulating rubber mats?
Electrical insulating rubber mats become the shield protecting from electrically conductive surfaces in electrically hazardous areas. These mats are made of neoprene, EPDM, or SBR and have high voltage resistance hence, they do not create electric shock and arc flash.
These mats are most often used in industrial locations, where electrical equipment, machinery, and power distribution systems are hazardous. Installing rubber insulating mats around electrical equipment and in electrically hazardous areas is a good way to protect employees and prevent accidents and injuries.
How to choose electrical insulating rubber mats?
- Standards compliance
Safety and effectiveness of the insulating rubber strip should be in accordance with the industry standards. ASTM D178 and IEC 61111 control the production of mats and their testing. These users have the confidence in the fact that a mat fulfilling these specifications has been purely tested and satisfies the electrical insulation requirements.
Moreover, some businesses need to put standards in place to ensure worker safety and compliance with regulations. Standard mats reduce the occurrence of electrical events and provide regulatory compliance through reliability and predictable performance.
- Voltage rating
Rubber mats should be at least or higher than the maximum voltage they will undergo. One of the safety measures for arc flash and electric shock is using a mat with an appropriate voltage rating. Select a mat with the safety margin enough based on your equipment's voltage class and voltage fluctuation.
For example, if your devices use 10,000 volts, then there is a suitable mat of a voltage rating of 15,000 volts that gives a safety barrier and accommodates voltage surges. Select a mat that is rated for the proper voltage grade to avoid electrical problems and risk the facility’s staff and equipment.
- Thickness
The electrical resistance of the rubber mat varies with the thickness of it. The high voltage and mechanical damage prevention that comes with thick mats are ideal for situations that have heavy foot traffic or are electrically risky. For safety and reliability, pick a thickness which goes with your equipment's voltage class and frequency of usage.
Thicker mats provide an additional cushioning effect which helps workers who stand for a long period of time relieve the strain. Also, the thicker mats stay longer and need fewer repairs. Workplace safety, comfort, as well as durability may be enhanced by opting for a thinner mat.
- Composition material
Neoprene, EPDM, and SBR are employed to make insulating rubber mats, which range in ozone, oil, chemical and temperature resistance. Choose the mat material for your specific working environment, its durability, and electrical insulation. If your facility is exposed to oils and chemicals, pick an oil-resistant mat to avoid deterioration and make the mat last longer.
Make sure to take into account your climate’s temperature range to select a material that won’t fail to work in severe temperatures. Select a mat featuring the material composition that both prevents electrical hazards and extends the life of the product as well as its operation in your intended application.
- Color-coding
Colored rubber mats may easily explain voltage levels and safety zones in a plant, making workers see the danger and obey instructions. A color-coded approach makes it easier to understand and streamline danger recognition, which ultimately helps reduce the risks of electrical accidents. To make sure there is clarity and efficiency, use colors that are widely identified and industry standard.
Think about using signs and labels with different colors in order to make it easier for workers to discover what color goes with what. A color-coded system will promote safety awareness and engender a safety culture in your company, and as a result, the number of electrical hazards, incidents and injuries will be lower.
- Durability and longevity
Buy high-quality rubber strip roll that can endure UV light, wetness, and temperature changes. Enhanced integrity, resistance to tearing and wear, and warranty against production faults ensure durability and reliability in electrical risks. Pick a mat depending on both its lifetime and application durability.
Add mats with beveled edges to prevent tripping, and securement solutions to make sure they are fastened. Rubber mats which are strong enough to make replacement and maintenance costs and downtime unnecessary and to ensure safety and protection of the facility.
- Test and inspect regularly
After installing the rubber strip, they must be tested and checked often in order to ensure their condition. Visually detect damages, wear and tears, and electrically test the carpets for voltage resistance. Have a maintenance program in place that addresses the issue straight away and replaces unsafe mats to keep the workplace safe.
While testing and inspection may identify issues early on but may prevent mat related accidents and injuries. For consistency and completeness, think about creating a formal inspection plan with well-defined procedures and trained staff. Motivating testing and inspection guarantees staff protection and security.
Conclusion
In electrical hazardous areas, it is important to have the right and appropriate electrical insulating rubber mat to protect both workers and equipment. Knowing your requirements, picking a product that is compliant with the current standards, ensuring the voltage rating, thickness, material composition and surface finish are considered, and prioritizing durability and life expectancy will be the key elements to make a decision that will promote electrical safety and reduce the pains of operating.
Related Courses and Certification
Also Online IT Certification Courses & Online Technical Certificate Programs